Re Slotting
Slotting and rearrangement concept :
In this article I will discuss a few points regarding Slotting and Re arrangement in a warehouse at a conceptual level.
Product Slotting is defined as the intelligent location of product in a warehouse or distribution center for the purpose of optimizing material handling efficiency. Sometimes called inventory slotting, or inventory profiling, it identifies the most efficient placement for each item in a distribution center or warehouse. Since each instance is unique, product slotting depends on. Before you begin a project for warehouse slotting, insure that you have aisles, bays, shelves and slots clearly marked with large and easily identifiable location signs. A slot can be part of a shelf or the entire shelf. Your Warehouse Management System (WMS) must reflect these storage locations for proper location control in your warehouse or DC. Re: Felder slotting cutter Michael Tagge #111416. Mark-Depending on which one it appears. One is 4, one is 5. Built Custom Carpentry Get Outlook for iOS. Dec 19, 2020 As per general understanding slotting is an the exercise of re arrangement of material into bins based on past statistical sales data.That is system will calculate the frequency of the material picked for sales order and determine if the current existing position of the material is most ergonomic to be picked.
It is a known fact that intelligent put away will result in efficient picking. Warehouse managers aim at storing material in a warehouse in a way that will help pick it in minimum time.
The material kept at a lower rack can be picked more easily then the one in a higher rack.
Hence at regular intervals ,a slotting and re arrangement exercise is done in order to arrange the material to be able to be picked fast.
Slotting is term we find introduced in SAP eWM .The following definition is from SAP help .
During slotting the system determines the underlying storage parameters that are relevant for put away on the basis of master data, that is, product data, requirement data, and packaging data. These parameters describe the storage section in which the product is to be stored, the properties that the storage bin is to have, and the putaway strategy that is to be used.

The requirement data is focussing on the projected demand of the product based on past data.
Re arrangement is the excercise moving of material from the bins to the most optimum bin from where it could be picked easily.This is done by looking at the picking frequency of the material and having the high velocity items arranged in the golden zone or so.
In terms of SAP WM standards simply put Slotting refers to the most ergonomic way of storing material in a warehouse to aid efficient picking .
As per general understanding slotting is an the exercise of re arrangement of material into bins based on past statistical sales data .That is system will calculate the frequency of the material picked for sales order and determine if the current existing position of the material is most ergonomic to be picked. If it is not, than move it to a more appropriate bin (re arrangement)
In Standard SAP WM we don’t have the direct slotting functionality available as tool.But if we look at it practically we have some form of slotting in the Fixed bin put away.
The fixed bins have min and max quantities marked.If the stock in the bins gets depleted it is replenished with stock from over flow bins (re arrangement)
Re Slotting Roofing
…to be continued
Note: All the logos, images, icons are the properties of the respective owners.1.0 Major Corporations
With a network of 12+ DC's, all across the US, Kimberly-Clark manufactures its products and distributes them. Facilities are large, in the range of 500,000 sq.ft.. We implemented layout improvements to reduce space lost due to honeycomb. A unique bulk pick line was designed and implemented. |
Constrained by a limited harvest season and space restrictions, we improved their layouts in 3 major DC's located in Ohio, California and Texas. In one location, we proposed to remove a tow-line and increase productivity. |
Our layout and slotting projects were in their Office products division. A key feature was the variable width slotting in their carton flow and static bins. These solutions were implemented in over 16 facilities in the US. |
Starting in Jacksonville FL, we redesigned the layouts using variable product height and footprints. Each appliance like a washing machine, refrigerator has its own unique dimensions and comes with its own package. We also designed an efficient pick line for the top movers. GE later implemented these concepts in 4 more facilities. |
Located in Mascot KY, GE's Electric products division, manages a 500,000+ sq.feet DC. Using our simulation and re-slotting techniques, we increased their picking productivity by over 15%. |
Colgate-Palmolive retained us to improve the storage and picking operations at a facility located about 25 miles north of Mexico City in Mexico. Following the success of this project, C-P invited us to perform similar projects in Cali Colombia and San Paulo Brazil. In these projects, we examined the various business channels for the different products. Installed both pick lines and efficient product storage layouts. |
We started a pilot project in Memphis TN. Our efficient product storage depths for bulk storage were not accepted first. We implemented them at the site and tracked the space usage for few months. The results came in line with our projections. With their green light, we implemented similar layouts and slotting at 10 more facilities. |
Through the acquisition of successful regional pickle companies, Deanhas grown in this business to become one of the two largest picklebusinesses in the U.S. Dean currently has 8 pickle processing plantslocated in Wisconsin, Michigan, Indiana, North Carolina, Georgia,Florida and Colorado.Our layout designs included labeled products as well as un-labeled finished sku's. These un-labeled products were labeled later based on demand. |
The main (and only) facility in Rogers Ark had not kept up with the changes in market demands. We removed their 4 deep and 8 deep drive-in racks and implemented a new layout that matched their product and ordering profile. |
The pilot project was conducted at their Davenport Iowa facility attached next to their manufacturing plant. We examined their manufacturing schedules and the inventory withdrawals. We installed the final layout and helped them achieve significant space and labor efficiencies. |
For a Nestle facility situated about 20 miles south of Mexico City, we examined their current layout, their product and demand profiles. We installed a better layout for that facility. |
AmeriServe was a major distributor of Food service products. They catered mainly to branded restaurant chains like KFC and others. Working with Argent Consulting, we helped to analyze the travel component involved in each order, both in the X,Y axis and the vertyical Z axis. These travel distances, accurate to an inch were used in computing the engineered standard times for the full picking activity. Implemented in over 25 facilities across the US. |
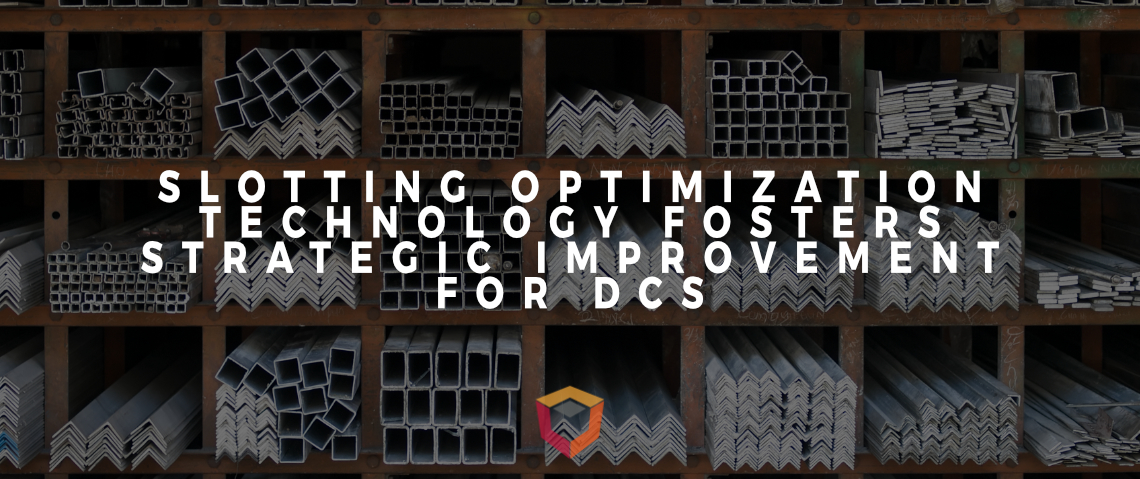
2.0 Other corporations
B.T.Office products International | Berry Plastics Corporation | Arden Fasteners |
Anderson Windows | The Antioch Company | Ames - Lawn and Garden Tools |
DSC Logistics | CSC - Computer Sciences Corpn. | General Mills |
Golden valley Microwave Foods | Harper Collins Publishers | Gopher Electronics |
Henry Schein | Graco | Hal - Leonard Corporation |
Setter Leach and Linstrom | Hennepin County | Lab safety Supply |
Lever Brothers Company | McKesson - Redline / Medimart | The Martin Brower Company |
Manhattan Beer Distributors | Ozburn-Hessey Logistics | Office-Depot |
Northland Electric | Nash Finch Company | Owens-Minor |
Pinacor | Peach State | Richfood |
Regis | Sabritas | West marine |
Update International | Viking Electric Supply | Hoffman Engineering |
Associated Grocers | Super Foods Services Inc | Pueblo Supermarkets |
CSI - Sporting Goods | Donalson - Filter manufacturer | Edward Don and Company |
Federal Cartridge Company | Fairway Foods | Foodland Distributors |
Georgia Pacific Corporation | Forward Enterprises Inc | Holiday Companies |
Land O'Lakes | Orgill Brothers | Rollerblade |
Rockport Company | CTI | Sigma Alimentos |
Shop Rite - Wakefern | Aldrich Chemicals | Seta Corporation |
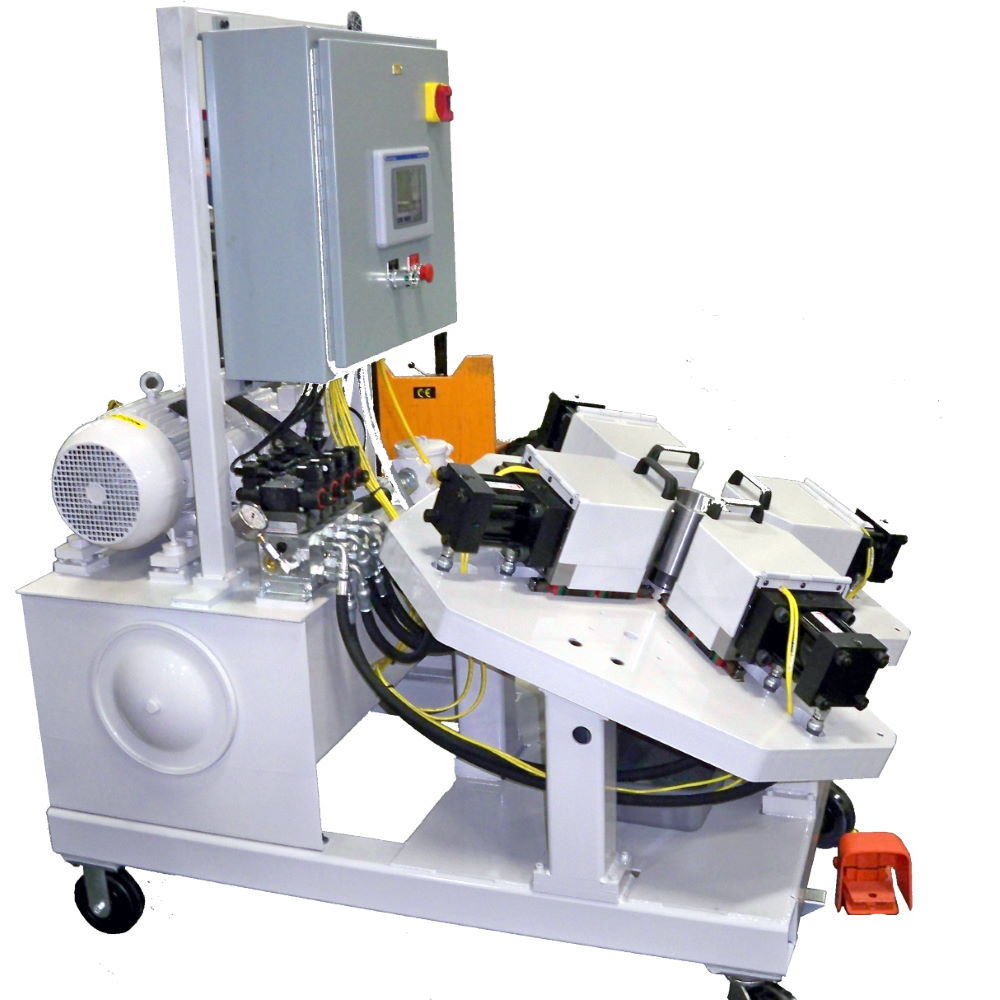
3.0 Outside USA
South America
4.0 Common types of applications
Improving an existing facility
Karma Logistics (KL) canexamine the layout, product slotting, material handling systemsand other related functions in an existing facility. Productivityimprovements resulting from the project usually consist of 12-16%increase in space utilization and about 10-20% reduction inoperating costs. These estimates may vary for a specific facility.
Karma Logistics hasassisted many Consumer Goods companies such as Kimberly-Clark,Campbell Soup, Colgate-Palmolive and many others to increaseproductivity in their operations.
Designing anew facility
When a new facility isbeing designed - either a green-field construction or an existingbuilding - this gives the company a major opportunity tothoroughly examine their business mix, customer servicerequirements and design a really good operation. Using thesimulation power of DC Optimizer computer software (software owned by Descartes Systems), Karma Logistics can examine alternate scenarios and installthe best design. Incorporating specific features to maintainflexibility is a must. Working hand-in-hand with a small team ofstaff from the facility, we can deal with the practical issuesand assure a smooth implementation.
KL has designed newfacilities both small and large, for companies like FederalCartridge, General Electric (Appliances), Colgate-Palmolive,Graco and others.
Reslottingthe products
Slotting the products inthe right way can reduce travel time, reduce product damage,increase percent of orders filled on time and complete.Simulating the different scenario allows Karma Logistics to select the best slotting scenario. The simulation model canpredict actual results within 5% variance.
Examples of productslotting assignments include many food retailing and wholesaledistribution operations. Super Foods, Pueblo Foods, Tyson Foods,Hunt-Wesson and others benefited from improved slotting in theirfacilities.
Fortune 100company with a major national network of DC's
Karma Logistics andthe Client company will select a pilot facility and commence theproductivity improvement process. Staring with a limited numberof changes, we build upon the successes incrementally. By thecompletion of projects at the 3rd and 4th facility, the essentialelements of the productivity improvement program are identifiedand we roll-out these techniques to other facilities in thenetwork.
General Electric(Appliances), Kimberly-Clark, Hunt-Wesson networks followed thisimplementation scheme.
Regionalsmall company with 1 facility.
Given the fact that thereis only 1 facility for the client, Karma Logistics willcarefully examine all the options, establish a long-range goal ofobjectives and install the BEST facility option.
Hal-Leonard Publishing,Rollerblade and others retained KL to improve their facilities.
Contact:: Karma Logistics Inc Minnesota
Please send your request toram.krishnan@karma-logistics-inc.comby completing the FORM below.